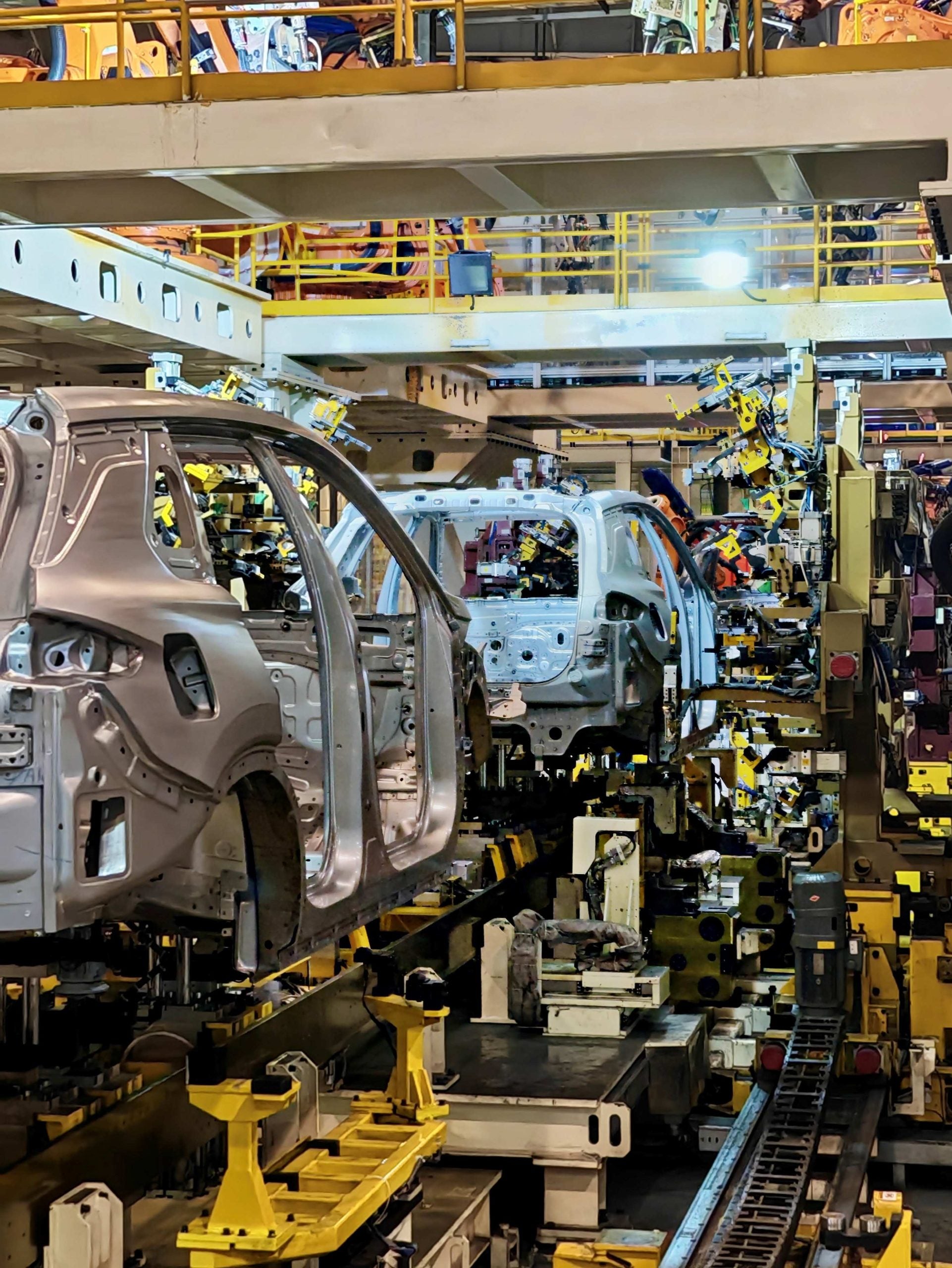
Stellantis unit Comau has supplied Hycan Automotive Technology (Hycan) with an intelligent welding system for its body framing line.
The innovative system is used for multi model manufacturing of new energy vehicles at a high JPH (Jobs per Hour) rate and with a “concrete” reduction in production losses.
Installed at Hycan’s Hangzhou factory, the flexible automated production system can randomly switch between four different platforms, is fully compatible with the existing manufacturing platforms and is used to build the brand’s BEV A06 sedan and Z03 SUV at a cycle efficiency of 60JPH.
In addition to facilitating seamless introduction, adaptation and scaling of new Hycan models, the system gives the automaker complete flexibility for the future.
The Hycan installation is based on a customised version of Comau’s Opengate framing system, which delivers flexible, high precision, body in white assembly, and virtual commissioning technology.
Comau also added a flexible servo positioning mechanism to the conveying system to help shorten the production cycle while ensuring both economy of scale and product diversification. With an OEE (Overall Equipment Effectiveness) exceeding 90%, the system has annual production capacity of up to 200,000 units. Because it can complete random mix production from one to six models, it allows Hycan to achieve true zero loss production.